In the aerospace industry, ensuring the integrity and safety of components is absolutely crucial. With the high costs and vital importance of maintaining structural integrity, the industry has turned to advanced imaging technologies to meet these needs. X-ray and Micro-CT technology have emerged as revolutionary tools that provide extraordinary insights into the internal structures and potential flaws of aerospace parts. These technologies enable more accurate and comprehensive assessments, essential for maintaining the highest standards of safety and performance in aircraft and spacecraft. This blog explores how the innovative solutions from KA Imaging, such as the Reveal 35C and inCiTe 3D X-ray microscope, are transforming aerospace non-destructive testing (NDT) by delivering detailed imaging that goes beyond what traditional methods can offer.
Importance of Quality Testing and NDT in Aerospace Industry
As an industry with safety at the forefront of their operations, non-destructive testing methods are pivotal to the aerospace industry. Aerospace components can experience many non-visible defects, and depend on NDT to ensure the safety of aircrafts, spaceships, and more. Destructive testing methods are not often utilized for aerospace, as aerospace components are extremely costly to produce. NDT gives aerospace companies the opportunity to perform quality testing while still maintaining the functionality of aerospace components, such as an aircraft’s elevator. This ensures that, if the component is considered viable, the components can continue to be used in everyday operations. Throughout the years, aerospace has prominently utilized several NDT methods to diagnose manufacturing defects.
Testing Methods in Aerospace NDT
There are many NDT methods that are commonly used within the aerospace industry:
- Ultrasonic Testing (UT): Ultrasonic Testing can be effectively performed on metal materials such as steel and iron. It sends short ultrasonic waves through a specimen to detect any audible discrepancies. Although UT is most functional with metal materials, it is also viable to be used with concrete or wood materials, although with weaker sound detection.
- Magnetic Particle Inspection (MPI): Magnetic Particle Inspection is used with ferromagnetic materials, most commonly iron, copper, and nickel. It can also be used on certain alloys or compounds that contain trace amounts of ferromagnetic materials. It determines defects like cracks beneath the surface of a specimen by running a magnetic current through it. The magnetic particles will accumulate at the site of cracks or discrepancies.
- Fluorescent Penetrant Inspection (FPI): Fluorescent Penetrant Inspection is a NDT technique designed to find surface defects in materials like metals or plastics, or any material that is non-porous. It involves applying a low viscous fluorescent dye to the surface of a specimen. The dye will seep into any surface cracks or discrepancies.
- Radiographic Testing (RT): Radiographic Testing is what KA Imaging specializes in. RT uses X-rays or gamma rays to create an image of the inside of a specimen. These images are then examined by specialists to identify abnormalities in structure and/or general defects. It is similar in practice to medical radiography, but instead examining objects and materials.
What is Micro-CT Radiographic Non-Destructive Testing?
Micro-CT, or micro-computed tomography, is an advanced imaging technique that produces high-resolution, three-dimensional images. It creates images of an object’s internal structure without causing significant damage or requiring dissection. It is essentially a scaled-down version of the standard computed tomography (CT) scans used in medical imaging, providing much finer detail. Micro-CT is employed extensively in scientific research, material science, biology, geology, and industrial non-destructive testing. In micro-CT, the object itself is rotated 360 degrees. As it rotates, X-rays pass through it from various angles, producing a three-dimensional image of the object.
What is SpectralDR technology for Non-Destructive Testing?
KA Imaging developed a patented cutting edge Dual Energy Subtraction technology known as SpectralDR. SpectralDR is unique from other DES technology because it acquires multiple energies in one X-ray exposure while not requiring increased radiation doses. The standard radiation dose needed for the average DR is all that is needed for Reveal’s technology to produce crisp imaging. Additionally, this imaging can be executed with no distortion or errors caused by motion.
Triple Stacked Layer Design
Single exposure dual-energy subtraction X-ray – our SpectralDR technology – is only possible because of Reveal’s distinctive triple stack design. Thanks to SpectralDR, our mobile X-ray detector is capable of simultaneously acquiring three images with only one exposure. The technology is capable of producing separated imaging on bone or soft tissue, improving clarity and reducing the chances of important visualization being obstructed.
This advanced technology enhances the identification of different materials and improves the detection of cracks, corrosion, and other critical defects in aerospace components. With its ability to produce clearer and more detailed images, SpectralDR ensures the structural integrity and reliability of aerospace parts, contributing to safer and more efficient aircraft maintenance and manufacturing processes.
What sets KA Imaging’s NDT products apart
Since 2015, KA Imaging has remained a trailblazer in the world of X-ray imaging. We streamline radiographic technology, creating various unique products in the realm of micro-computed tomography, high-efficiency X-ray area detection, and multi-energy spectral separation detection.
KA Imaging supports aerospace use cases with our Reveal 35C X-ray detector and inCiTe 3D X-ray microscope. Reveal 35C is the first portable dual-energy single exposure X-ray detector, capable of single exposure dual-energy imaging. Reveal 35C generates three image types, traditional dr, and then two other images which highlight the low-density or high-density materials. This allows for advanced material separation for more comprehensive inspection. InCiTe pairs with Reveal 35C to offer phase contrast and micro-CT. InCiTe can provide enhanced visualization of low-density materials with its superior contrast, as well as producing three-dimensional images with its micro-CT technology. InCiTe uses propagation based X-ray imaging for enhanced visualization of objects with poor x-ray absorption.
KA Imaging’s products offer a distinct and customizable visual representation of an object’s structure. Radiographic inspectors can use Reveal 35C’s software to customize between focused imaging prioritizing high or low density material detection, or traditional imaging. Additionally, Reveal 35C uses single exposure, removing the appearance of motion artifacts which can disrupt visualization.
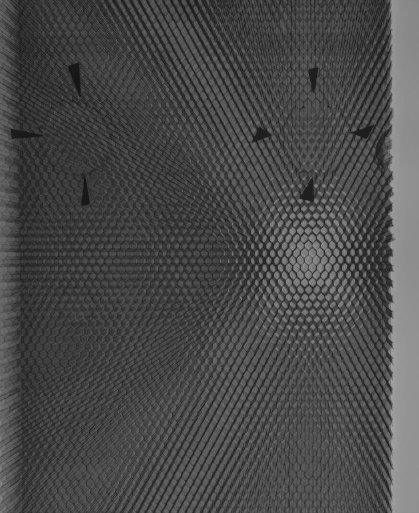
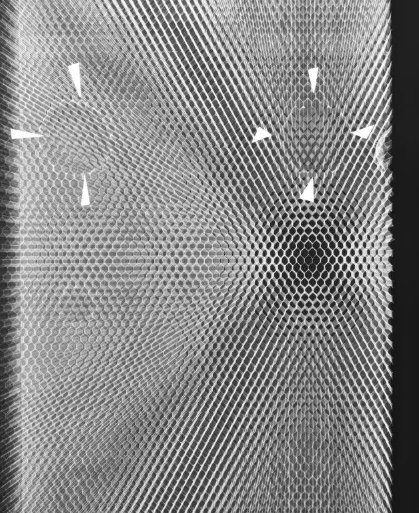
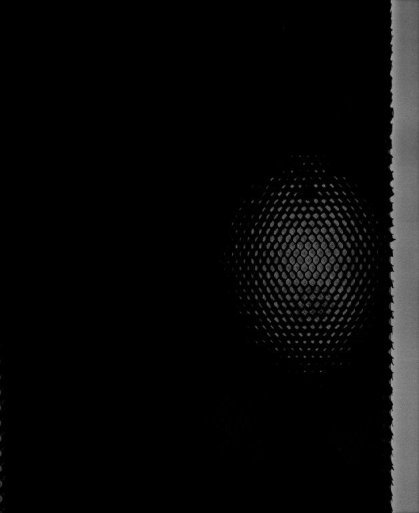
In the above image of a titanium composite wing, you can see a conventional DR image on the left paired with a low Z application in the middle, and high Z application on the right. Changes in matter caused by increasing or decreasing Z can affect photoelectric absorption
With technology like Reveal and inCiTe, aerospace quality testing can reliably produce more comprehensive imaging of structurally complex components. While other NDT methods give a partial impression of object discrepancies, KA’s radiographic technology offers clear, three-dimensional imaging that leaves a permanent record in the form of radiographic film or digital images. This record allows images to be repeatedly inspected for reinforced accuracy when detecting discrepancies.
Learn more about Reveal Technology.
Learn more about inCiTe 3D Technology.
Revolutionizing Aerospace NDT with KA Imaging
The integration of X-ray and Micro-CT technology into aerospace non-destructive testing represents a significant advancement in the industry. By offering high-resolution, three-dimensional imaging, these techniques provide a more complete and nuanced understanding of material integrity compared to traditional methods. KA Imaging has been at the forefront of this revolution, with innovative products like the Reveal 35C and inCiTe 3D X-ray microscope setting new benchmarks for accuracy and efficiency in aerospace NDT. These technologies not only enhance the detection of potential defects but also ensure that components can be safely and effectively used, thereby reducing costs and improving operational reliability. As the aerospace industry continues to evolve, the adoption of advanced imaging techniques will play an increasingly crucial role in maintaining the highest levels of safety and performance. Explore KA Imaging’s groundbreaking solutions today to find out how Reveal and inCiTe can elevate your aerospace quality testing processes.